Coconut Shell Charcoal Production: A Journey to Sustainable Briquettes
Coconut shell charcoal is a remarkable eco-friendly product with a wide range of applications. Have you ever wondered how this sustainable fuel source is made? In this article, we will take you on a detailed journey through the production flow of coconut shell charcoal, unveiling the meticulous steps involved in transforming coconut shells into eco-conscious briquettes. Let’s explore the fascinating process of turning waste into valuable fuel.
1. Crushing Process: Breaking Down the Shells
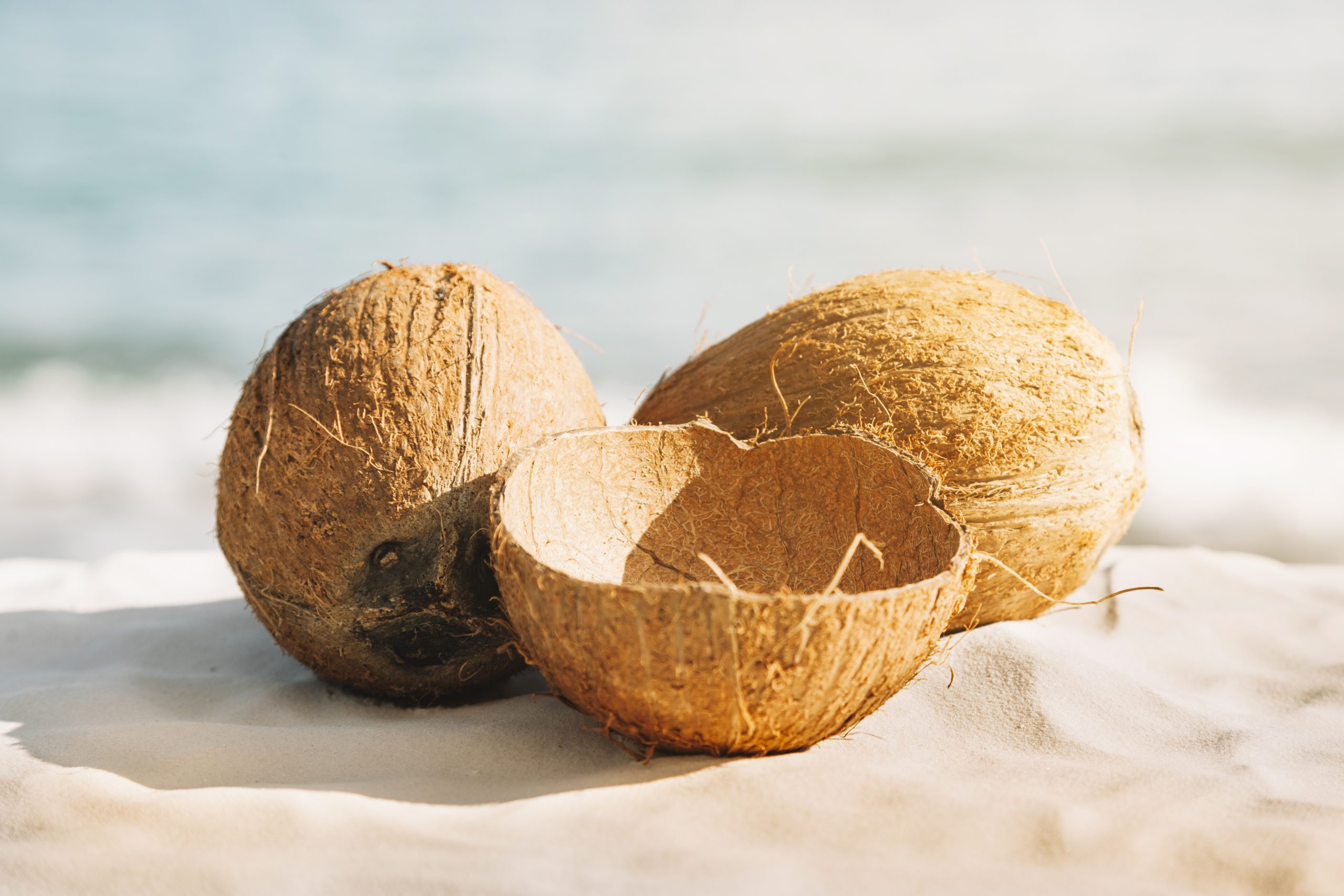
The journey begins with the crushing process, where a crusher machine breaks down coconut shell charcoal pieces into a fine powder, ensuring that the resulting charcoal is smaller than 3mm in size. This crucial step prepares the raw material for further processing and ensures that the charcoal powder is of the right consistency for the next stages.
2. Mixing Process: Creating the Perfect Blend
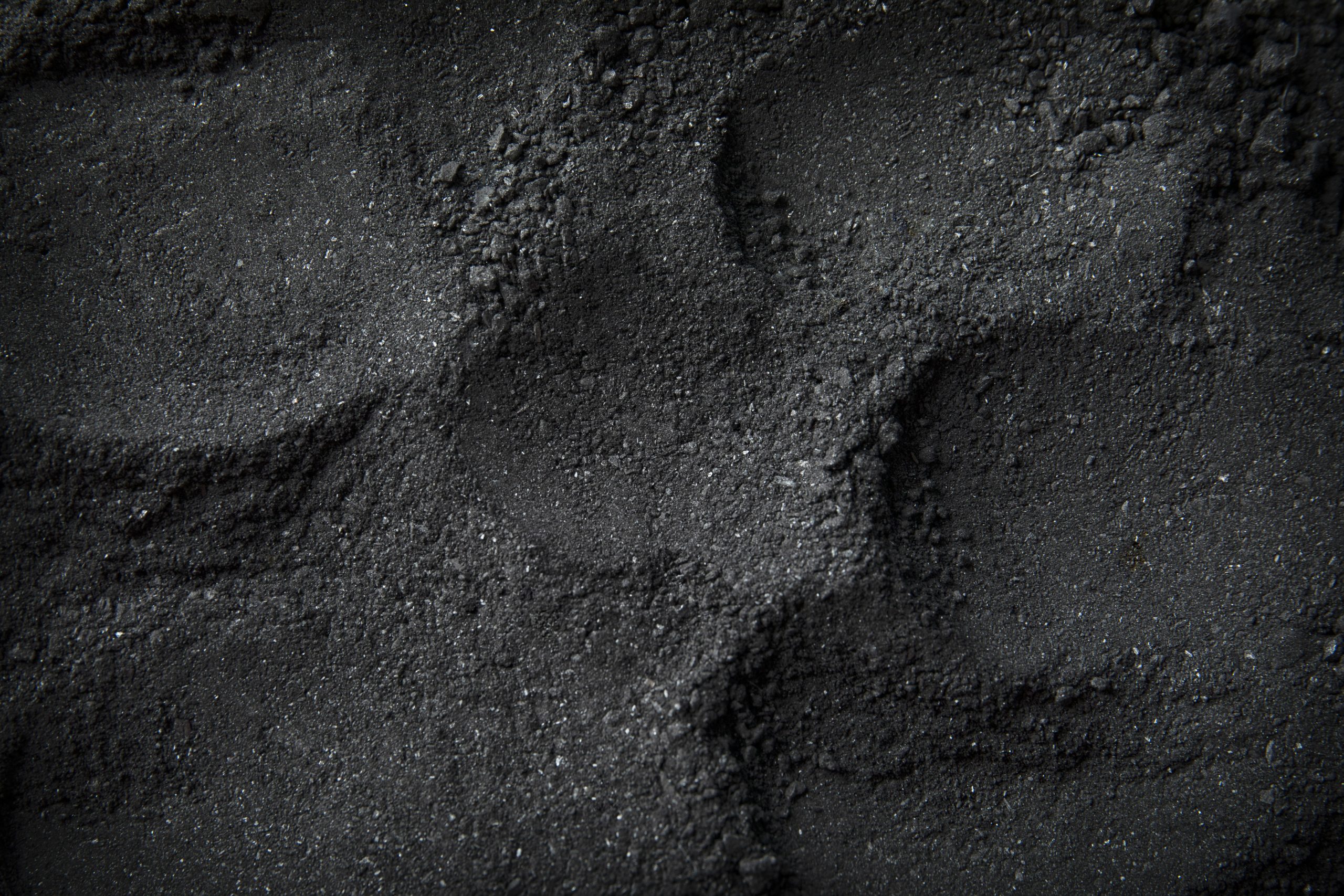
Next comes the mixing process, where the coconut shell charcoal powder is expertly combined with 5% food-grade tapioca flour and water. This perfect blend is mixed in a high-quality mixer machine for 25 minutes. The meticulous mixing ensures that the charcoal powder and tapioca flour are evenly distributed, creating a cohesive mixture that will later be molded into briquettes.
3. Blending Process: Transforming into a Cohesive Substance
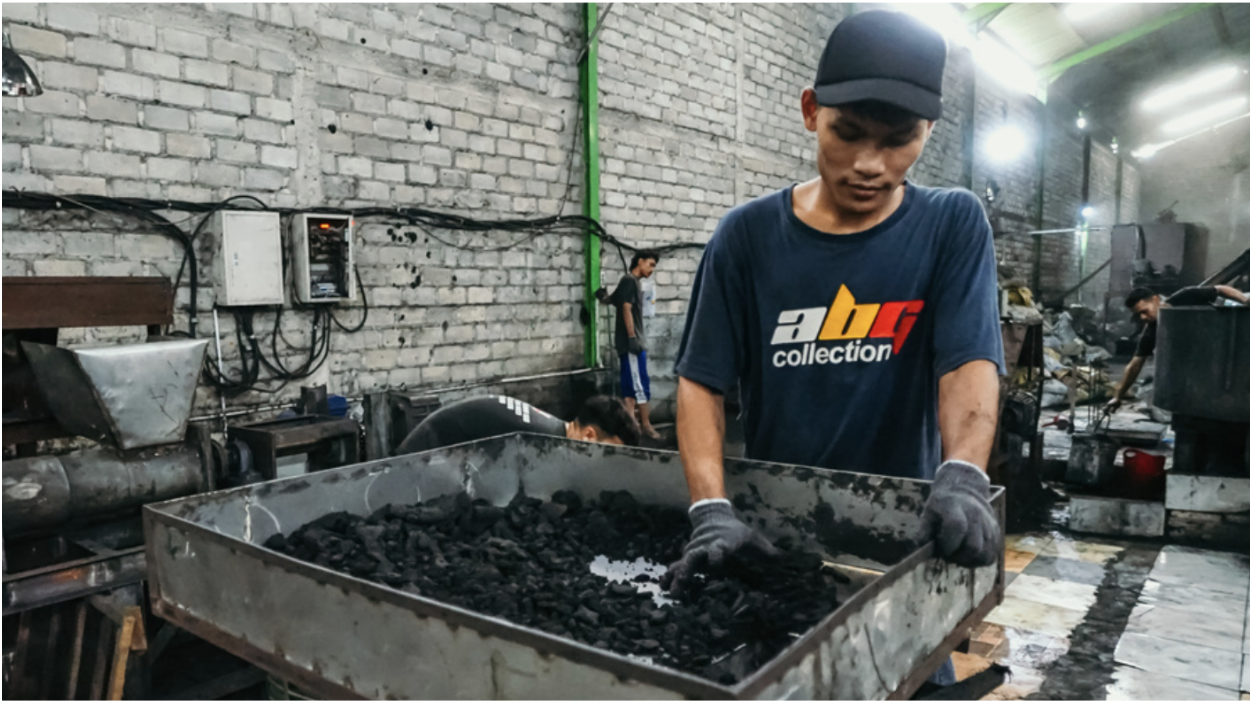
During the blending process, the wet mixture of coconut shell charcoal powder and tapioca flour undergoes a two-step blending procedure, resulting in a pastelike substance. Applying heat activates the tapioca flour, acting as a natural glue to bind the mixture together. This unique blending method ensures that the briquettes will have the perfect consistency and strength once molded.
4. Molding Process: Shaping to Perfection
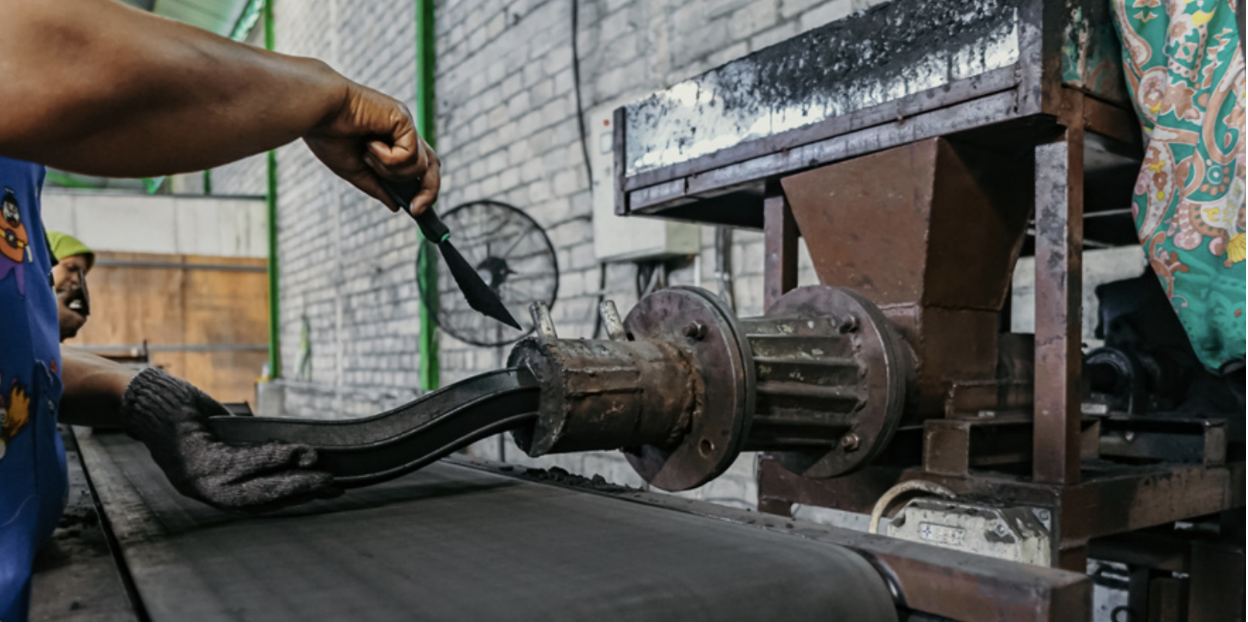
The blended mixture is carefully molded after several hours of cooling. Skilled workers use precision machinery to shape the charcoal mixture into briquettes of various sizes and shapes, customized to meet the specific requests of customers. This step plays a vital role in determining the final appearance and usability of the coconut shell charcoal briquettes.
5. Drying Process: Reducing Moisture Content
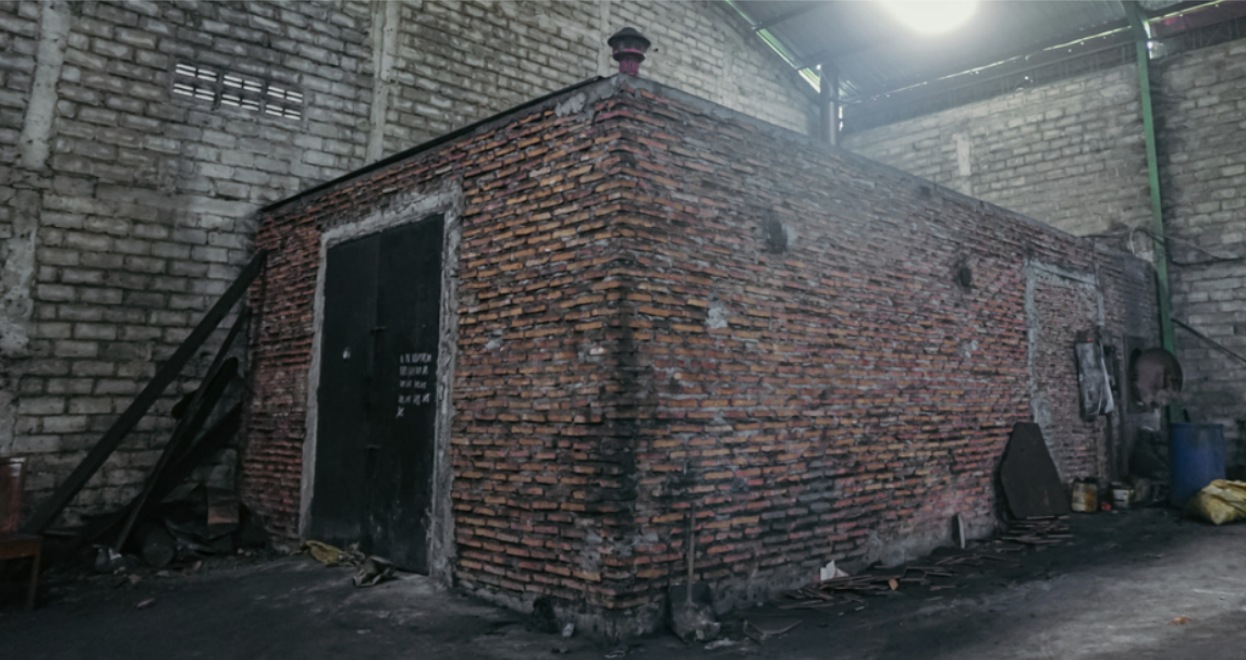
To enhance the quality and longevity of the briquettes, they are dried in an industrial oven for 48 hours. This meticulous drying process reduces the moisture content to 5% or less, ensuring the briquettes burn efficiently. The controlled drying conditions preserve the integrity of the briquettes, preventing them from cracking or breaking during use.
6. Packing Process: Preparing for Delivery
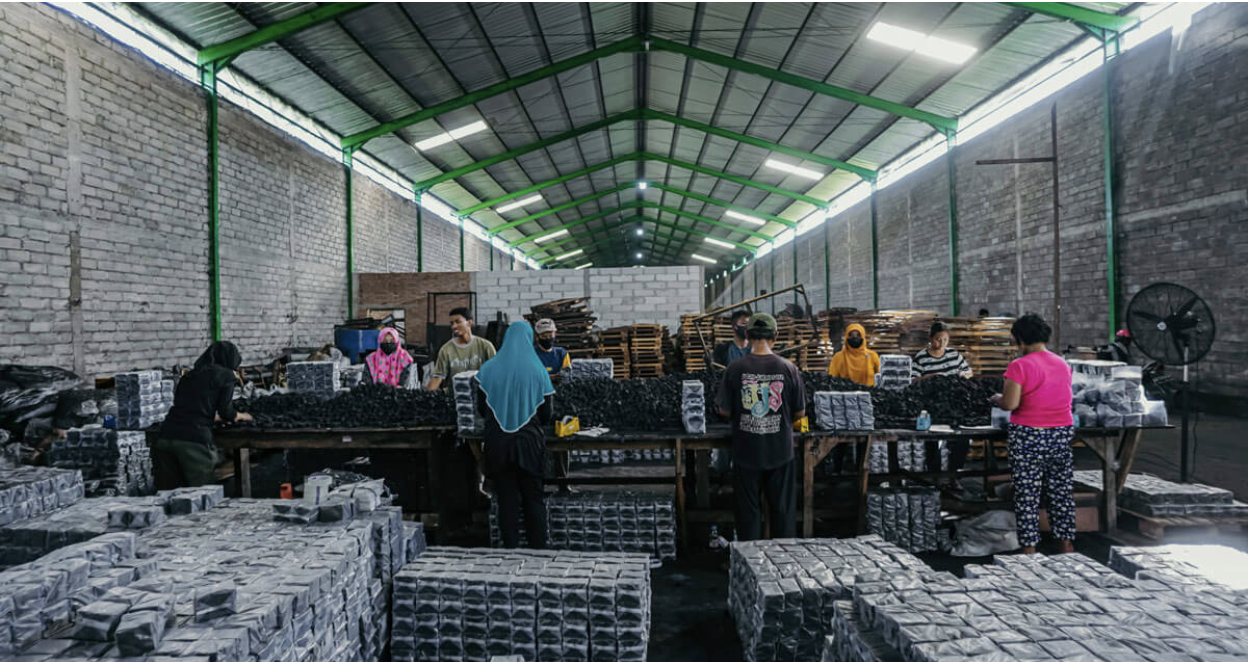
In the final stage of production, the briquettes are expertly packed into inner plastic, inner boxes, and master boxes, all designed according to the branding specifications of each customer. This ensures the safe and efficient delivery of the end product. The careful packaging also allows for easy storage and transportation of the coconut shell charcoal briquettes.
By understanding the production flow of coconut shell charcoal, we gain valuable insights into the intricate process of creating this sustainable and eco-friendly fuel source. From breaking down coconut shells to molding the perfect briquettes, each step showcases the commitment to preserving the environment and utilizing natural resources responsibly. The result is a product that not only meets the highest standards of quality but also aligns with the growing demand for eco-conscious solutions.
In conclusion, the production of coconut shell charcoal involves a series of precise and well-executed processes that transform raw materials into eco-friendly briquettes. This sustainable fuel source has a multitude of applications, ranging from grilling and barbecuing to industrial heating and water purification. Embracing coconut shell charcoal as an alternative to traditional charcoal not only benefits the environment but also offers superior performance and value. Join the movement towards a greener and more sustainable future by choosing coconut shell charcoal for your energy needs.